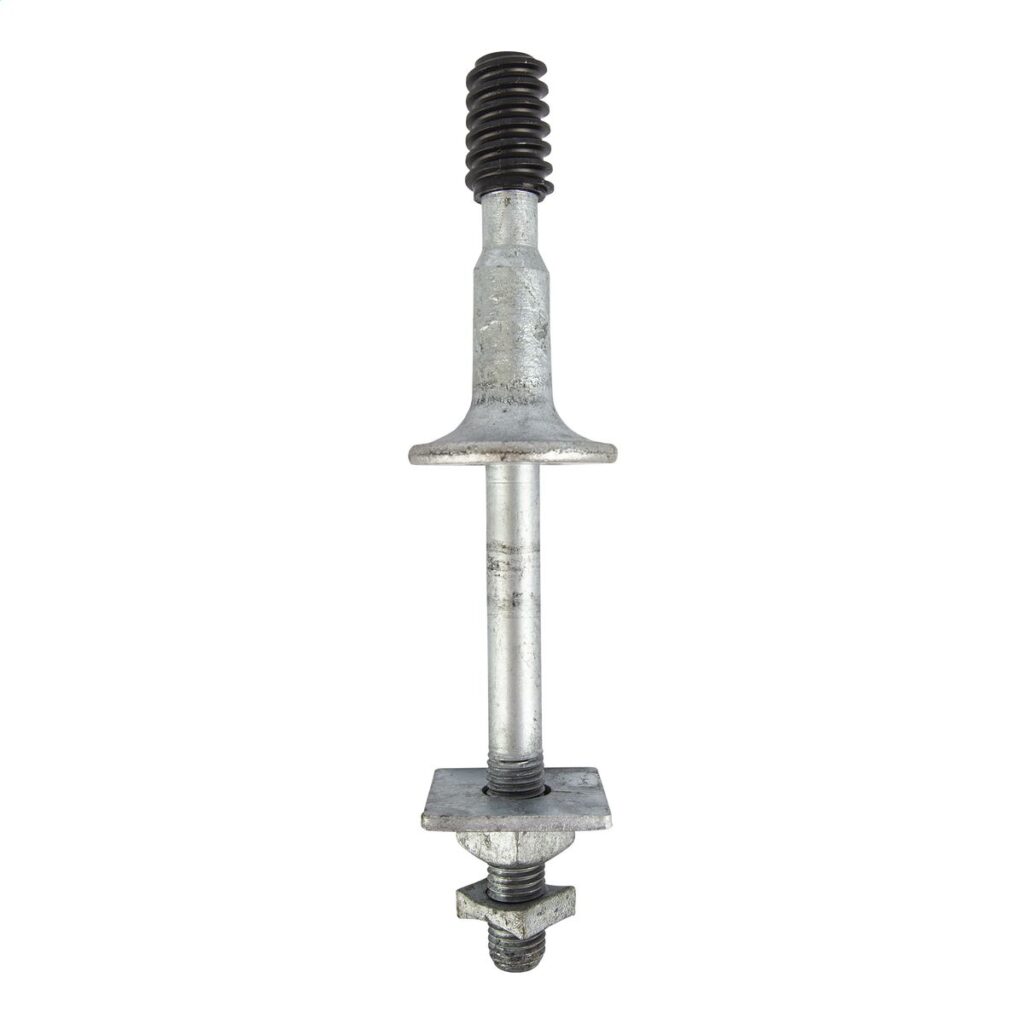
An insulator pin serves in supporting electrical conductors while ensuring they remain insulated. It is from durable materials designed to withstand the environmental stresses of outdoor use. It has a threaded end or a clevis to hold the insulator in place. Insulator pin’s main function is to serve as mounting points for insulators to maintain the integrity. They also suspend conductors while providing electrical insulation from the support structure. The top of the pin has a mechanism to attach the insulator. It includes grooves or a hole where the insulator fittings secure using a bolt. Using insulator pins helps to prevent electrical faults and ensure safe electricity transmission. They prevent electrical leakage, short circuits and other hazards.
Common types of insulator pin
The insulator pins are available in different types and designs to meet the specific requirements of the application. The selected type depends on the voltage levels, environmental conditions and mechanical loads. Additionally, consult with industry professionals for guidance on the best types. This is to ensure the safety, reliability and efficiency of the transmission line operation. The following are the common types of insulator pins used on overhead transmission lines.
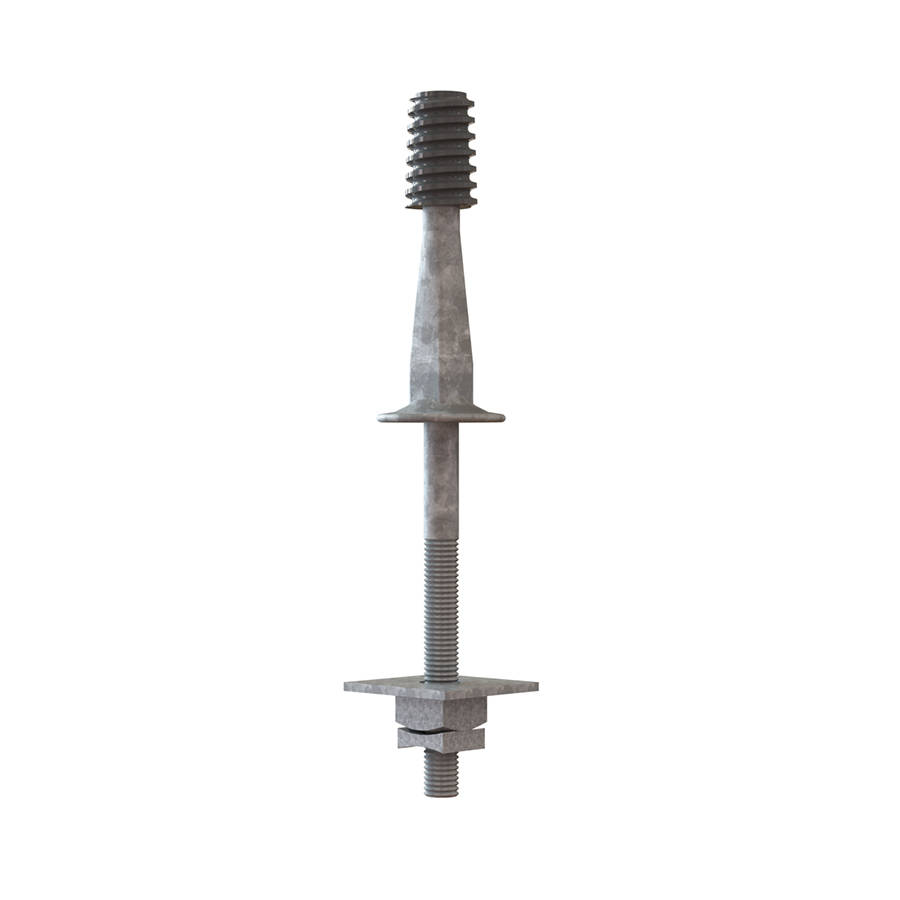
- Straight shank insulator pin – this pin features a straight shank that mounts onto the crossarms. They work in low to medium voltage distribution lines.
- Single-shedded insulator pins – these pins have one shed which projects part of the insulator body. This is to increase the surface area of water drainage. They work in low voltage applications.
- Square shank insulator pins – these have a square cross-section that offers stability and resistance to twisting. This is as compared to round shank pins and work in medium to high voltage transmission lines.
- Double-shedded insulator pins – these have two heads which provides more surface area for water drainage. It makes them more suitable for higher voltage applications.
- Threaded insulator pins – the pins have threads at the top to allow for direct attachment without need for fasteners. They provide a secure connection and work in high voltage applications.
- Composite insulator pins – these are from a combination of materials such as porcelain and fiberglass. This makes them lighter and stronger than traditional porcelain insulator pins.
- Ball and socket insulator pins – the pins feature a ball and socket joint at the top for flexibility and reduce stress concentrations. They work in areas with high wind or vibration.
- Insulator pins with anti-fog coating – these are insulator pins coated with a special substance. The coating helps prevent the formation of fog on the insulator body. This can reduce the risk of arcing on the transmission lines.
- Clevis insulator pins – the clevis pin has a U-shaped fitting at the top which allows for easy attachment of the insulator. They are versatile and work in various voltage levels.
Differences between an insulator pin and a pin insulator
A pin insulator is a type of insulator used to support and insulate electrical conductors from the support structure. It consists of a porcelain or glass body in the shape of a cylindrical spindle with a grooved top to hold the conductor. Its main function is to provide electrical insulation between the conductor and the support structure. The insulating material used in the pin insulators has high resistance to electrical current. Also, it is advisable to understand the differences between the insulator pin and the pin insulator before selecting. The following are the various differences between the two.
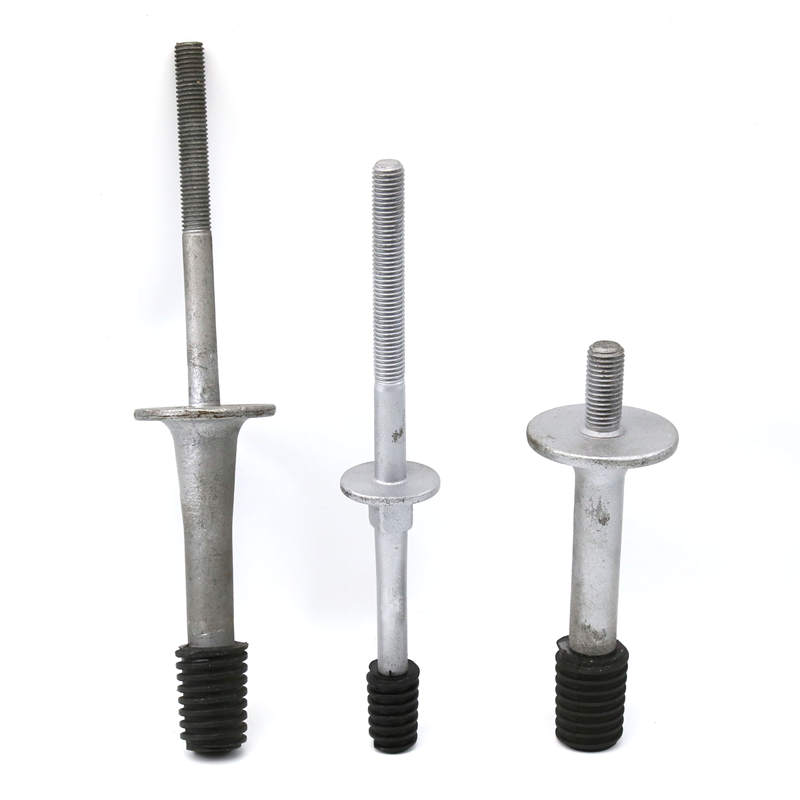
- Function – an insulator pin support insulators and ensure proper electrical insulation between conductors. A pin insulator helps to provide electrical insulation between conductors and support structure. It prevents electrical current from flowing through the structure.
- Material and design – insulator pins are from materials like steel, aluminum or composite materials. Their design varies depending on the specific application requirements. pin insulators are from materials like porcelain or glass. They have a cylindrical shape with a grooved top to hold the conductors.
- Attachment – insulator pins feature a mounting mechanism at the top such as threads or clevises to attach the insulator. They mount onto crossarms and provide the interface for connecting insulators to the overhead lines. pin insulators mount on insulator pins which then attach to the crossarms or support structures.
- Insulation – the main purpose of the pin insulator is to provide electrical insulation. It also ensures the electrical current flows through the conductor.
Advantages of using insulator pins
Insulator pins offer several advantages which contribute to the reliability, safety and efficiency of the electrical infrastructure. Using insulator pins provides electrical insulation, mechanical support, durability and cost effectiveness. These advantages make insulator pins essential components for ensuring reliability and efficiency. The following are the advantages of using insulator pins.
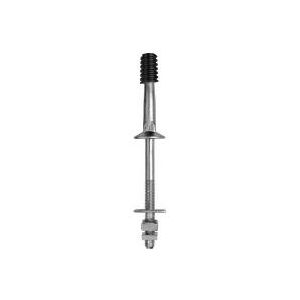
- Electrical insulation – insulator pins provide essential electrical insulation between the conductors and support structures. This prevents electrical current from flowing through the structure to maintain the integrity of the electrical system.
- Versatility – insulator pins are available in various design and configurations to fit different applications and voltage levels. They work in a wide range of environmental conditions and are compatible with different types of insulators.
- Cost-effectiveness – the pins are cost effective in design and construction which makes them cheap for insulation.
- Compatibility – the pins are compatible with various types of insulators. This allows for seamless integration into different systems. This ensures interoperability and eases system upgrades.
- Mechanical support – the pins offer mechanical support for insulators to ensure they remain attached to the support structure. This prevents sagging or movement of the conductors to maintain proper clearance.
- Durability – insulator pins are from durable materials such as steel, aluminum or composite materials. They help to withstand environmental stresses including weather conditions, wind and temperature fluctuations.
- Ease of installation – insulator pins are easy to install and can mount onto crossarms or other support structures. This makes the installation simple and reduces labor costs related to overhead construction.
- Safety – the pins contribute to safety of overhead electrical systems by preventing electrical faults. They also reduce the risk of accidents. Using insulator pins helps to protect workers, public and the environment from electrical hazards.
Cost comparisons and considerations for insulator pins
There are several factors that influence the prices of the insulator pins in the market. These factors include material, design complexity, quantity discounts and installation costs. The sots of the insulator pins should balance upfront investments with long-term value and performance. Additionally, it is advisable to consult with stakeholders and suppliers to get the best prices. Current prices for insulator pins in the market range from $0.60 – $5.20 depending on order pieces. The following are the factors that influence the price of the insulator pins.
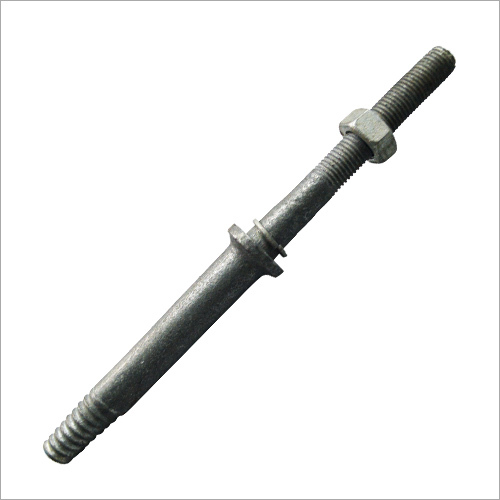
- Material – the materials used in the construction of the insulator pins impacts their costs. Steel insulator pins are less expensive compared to aluminum or composite pins. Each of these materials offer different advantages to it is advisable to carefully consider when selecting them.
- Quantity and volume discounts – purchasing in large quantities results in volume discounts from suppliers. Also, long-term contracts or partnerships with suppliers may lead to discounted pricing arrangements.
- Life cycle costs – consider the lifecycle of the insulator pins including initial sale, installation, maintenance and replacement expenses. Check the total cost of ownership over the expected lifespan of the insulator pins.
- Design and complexity – simple designs with standard features are more cost effective. This is as compared to specialized designs. The complexity of the manufacturing process and the precision required for the designs can drive up production costs.
- Installation and maintenance costs – it is important to factor in installation and maintenance costs over the lifespan of the pins. Consider factors such as ease of installation, compatibility and durability.
- Environmental factors – exposure to corrosive elements, extreme weather conditions or high pollution can influence the costs of the pins. Select insulator pins made from materials enhanced with corrosion resistance.
Challenges and issues facing the insulator pins
Insulator pins are important in transmission systems but they face various challenges and issues. They can impact their performance, reliability and safety in various application areas. Additionally, the challenges need proactive measures to enhance durability and performance. The following are the common challenges and issues facing the insulator pins.
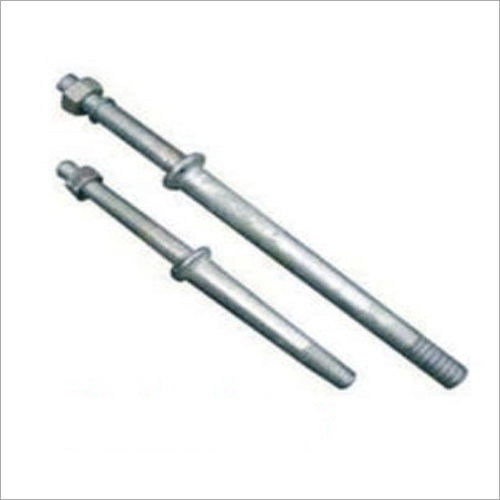
- Aging infrastructure – aged infrastructure may experience increased rates of mechanical failure, corrosion or material degradation.
- Mechanical stress – the pins are subject to mechanical stresses from various sources including wind loads, conductor tension and ice. This may compromise their ability to support the conductors and maintain proper electrical clearance.
- Overloading – the pins face overloading due to factors such as excessive conductor tension and winds. Overloading can exceed the design capacity of the insulator pins and lead to mechanical failure.
Frequently asked questions
A pin insulator is an insulating component used to provide electrical insulation between conductors and support structures.
The advantages include electrical insulation, mechanical support, versatility, durability, ease of installation and compatibility.
Common challenges include mechanical stress, corrosion, insulator contamination, overloading, material degradation and installation errors.