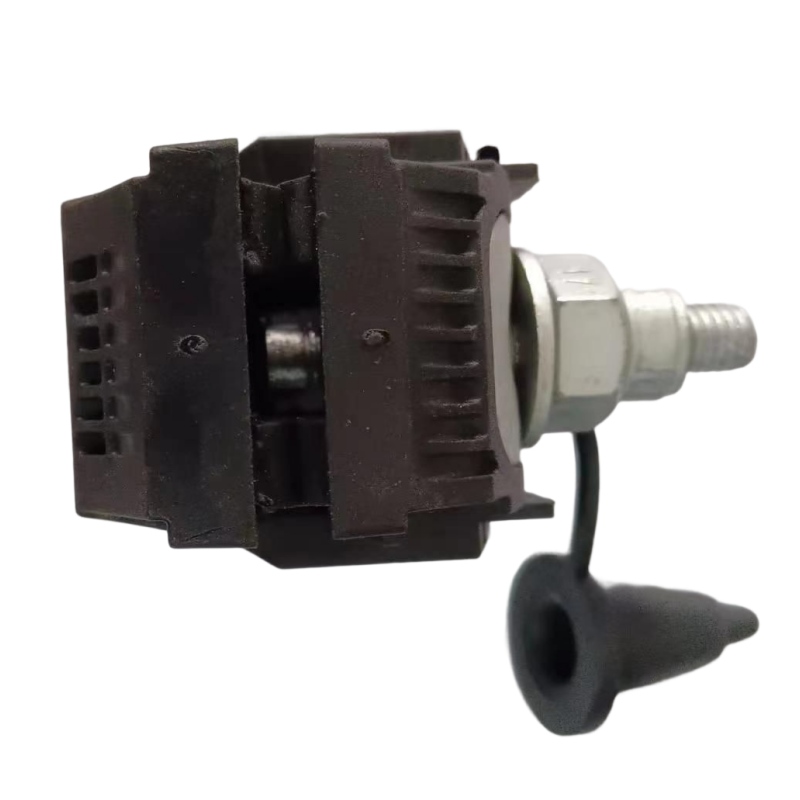
In high voltage power transmission networks, electrical connections use an insulated piercing clamp. It connects to the overhead wires that are already in place without de-energizing the line. Another name for an insulated piercing clamp is an insulated piercing connector (IPC). The sharp point of the clamp punctures the conductor’s insulation. This ensures a safe electrical connection without revealing the wire. By means of gripping mechanisms, it maintains its position even in the face of strong gusts. To prevent electric shock to the workers, the clamp also has insulated handles. The bolted IPC, compression IPC, tap connections and slicing connectors are the common types of insulated piercing clamps. They work in renewable energy systems, construction, and telecommunication.
Typical components used to create insulated piercing clamps
A wide range of materials work in the production of insulated piercing clamps. The particular design, intended use and desired clamp qualities all influence the material choice. Every material must attempt to fulfill the particular specifications and norms required for the intended use. The common materials used to make insulated piercing clamps are as listed below.
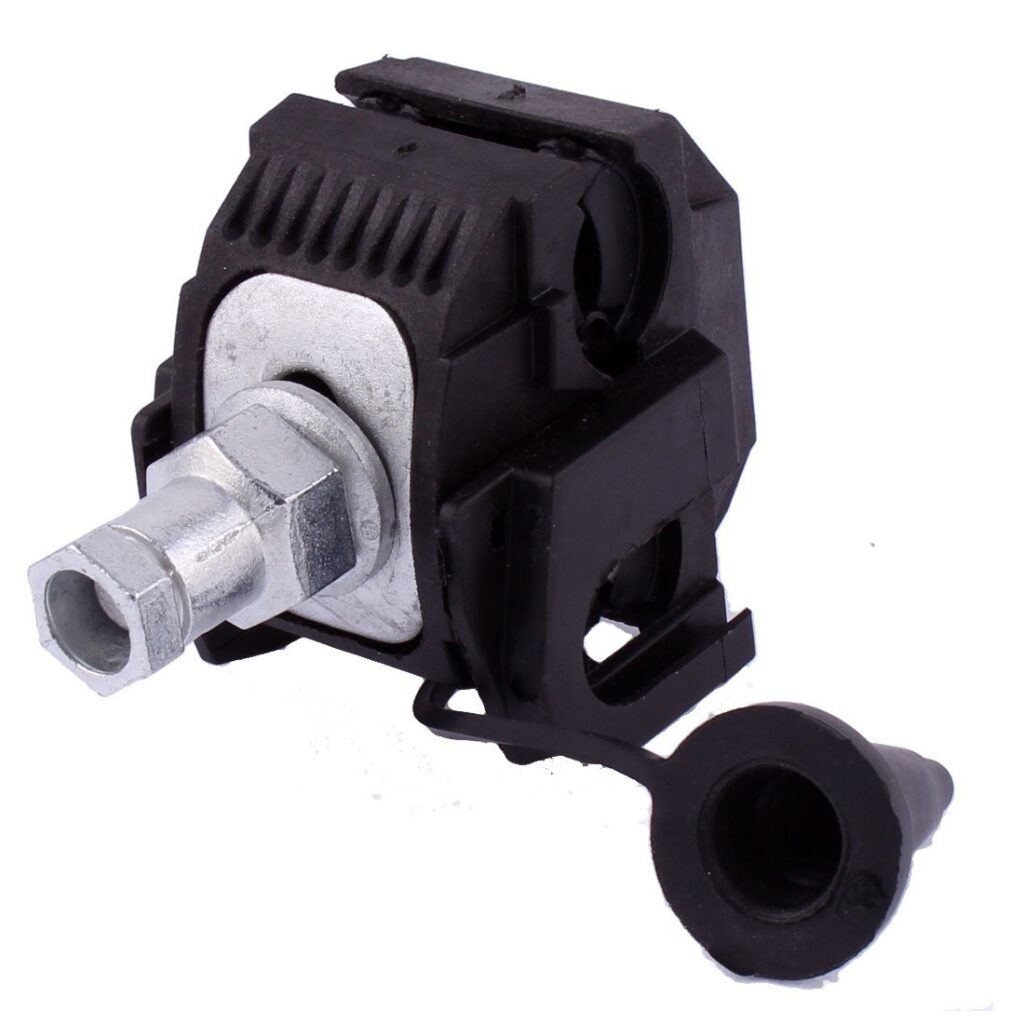
- Metal alloys – the clamp’s body is from sturdy metal alloys like brass, aluminum or stainless steel. They offer conductivity, strength and resistance to corrosion. This is to guarantee the clamp’s durability and dependability.
- Copper – the point that pierces wire insulation is also known as a piercing tip. It is from a sturdy, sharp substance like brass, copper or hardened steel. They guarantee the penetration’s effectiveness and consistent electrical contact with the conductor.
- Sealing materials – to stop moisture intrusion, they could use rubber or silicone sealing materials. In challenging environmental circumstances, it also guarantees the integrity of electrical connections.
- Coatings – certain components have zinc plating or powder coating. This will improve appearance, corrosion resistance and longevity.
- Insulating materials – on-conductive materials help to make the handles and insulation barriers on the clamps. These materials consist of rubber, nylon, or PVC. To prevent electric shock, the materials offer electrical insulation.
- Fasteners and screws – the clamps have stainless steel bolts, screws and other fasteners. This keeps the clamp in position and ensures that the wire is in touch with it.
- Polymers and plastics – these are useful in insulating bushings and housing covers. Extra insulation, impact resistance and weatherproofing are through the polymers or plastics.
Features of connectors with insulated piercings
Insulated piercing clamps are essential instruments due to some their features. For technicians, engineers and electricians, they are essential tools. The clamps offer dependability, efficiency and safety for connecting electrical devices. When choosing the IPC, it’s also crucial to look over the available properties. The common characteristics of insulated piercing clamps are as follows.
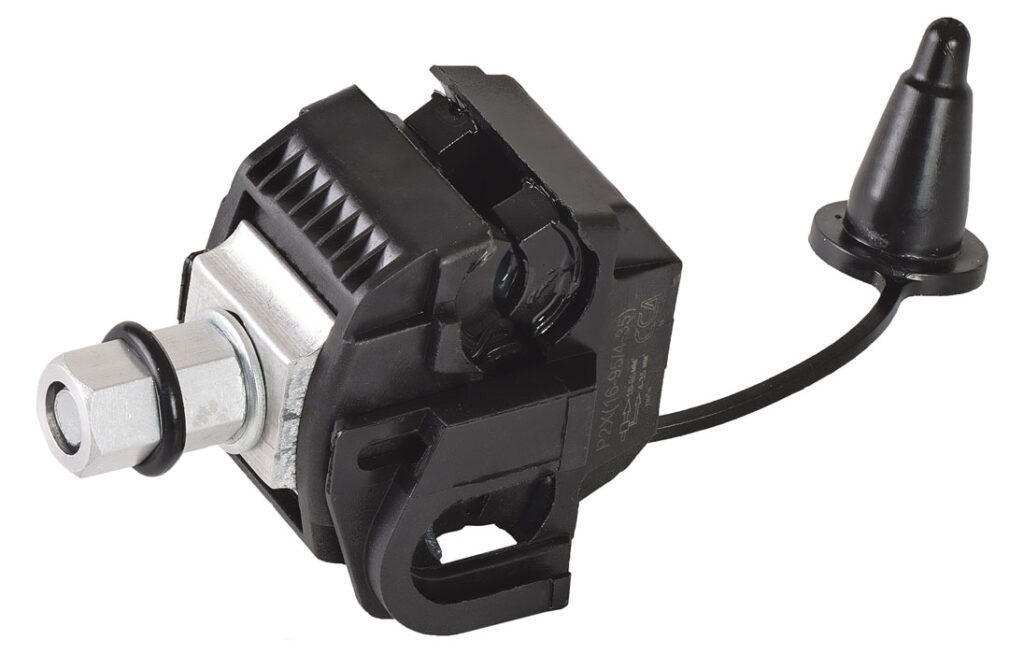
- Electrical insulation – non-conductive materials help to make the handles and insulation barriers on the clamps. These consist of rubber, nylon and PVC. This lowers the chance of short circuits and avoids electric shock.
- Durability – materials like brass, aluminum or stainless-steel work in making the clamps. The materials offer durability, strength and resistance to corrosion. This guarantees that the clamp will not break under the rigors of electrical work.
- Usability – the clamps’ handles and wire-piercing and clamping mechanisms make them simple to operate. This facilitates the process of connecting electrical devices. It accomplishes this by cutting down on installation time and effort
- Safety features – to prevent people from receiving an electric shock, the clamps incorporate safety safeguards. They lessen the dangers associated with handling live wires and help to guarantee dependable connections.
- Tip – the tip of a conductive piercing is from steel, brass or copper. As a result, the clamp may make an electrical connection with the conductor inside the wire.
- Weatherproofing – to keep out moisture and dust, the clamps have sealing materials.
- Versatility – a large variety of wire sizes and types work with the clamps. They can thus be useful in a variety of electrical applications.
- Reliability – the clamps establish safe, dependable electrical connections as well. This is to keep electrical circuits continuous and ensure proper conductivity.
Insulation of the IPC
In electrical systems, the insulation of an insulated piercing clamp serves many functions. It keeps dependable connections, guards against short circuits and guarantees electrical safety. Making the right insulation design and material selection is also crucial. This is to guarantee the clamps’ functionality and effectiveness. The clamps’ common insulating features include the following.
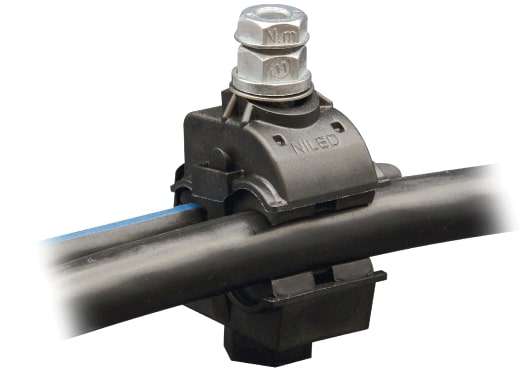
- Insulation – insulation prevents accidental contact between conductive parts, hence providing protection against short circuits. Electric current flows through the designated lines thanks to the insulation. Additionally, it keeps the electrical circuits’ integrity intact.
- Material selection – non-conductive materials like rubber, nylon, and PVC work as insulation. The materials are highly durable, resistant to external influences and have good electrical insulating qualities.
- Electrical safety – the primary purpose of the insulation on the clamp is electrical safety. The operator remains prevented from coming into direct touch with live wires by the insulation barriers and insulated handles. Additionally, it reduces the possibility of electric shocks occurring during maintenance, repair or installation.
- Environmental factor resistance – the insulation can tolerate a range of environmental conditions. These elements include temperature swings, chemicals, dust and moisture.
- Adherence to safety regulations – the clamps must meet particular safety norms and guidelines. This is to guarantee that they will guard against short circuits and electric shock.
The ability of insulated piercing clamps to resist corrosion
Since they work in outdoor settings, corrosion-resistant, insulated piercing camps are essential. The particular materials employed in the various clamp components affect their corrosion resistance. Their dependability and longevity in outdoor depend on this characteristic. Material, coating and sealing mechanism selection affects the IPC’s ability to withstand corrosion. It is also observed on the camp body, bolts, nuts insulation, and wedges. Corrosion resistance is important in electrical applications in the following ways.
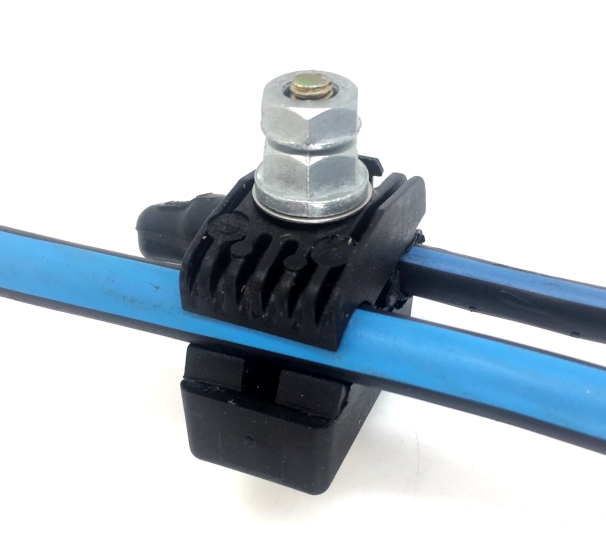
- Coatings – the clamps may be zinc-plated or coated with powder coatings. This will increase their resistance to corrosion and add another layer of defense against abrasive materials, chemicals and moisture.
- Corrosion – correct installation may involve making sure that all fastenings are snug and that the components align. By doing this, the chance of corrosion in insulated piercing clamps may decrease.
- Material selection – the selection of materials affects how resistant they are to corrosion. Materials that resist rust and corrosion include brass, stainless steel aluminum and other corrosion-resistant alloys.
- Sealing mechanisms – materials like rubber or silicone stop moisture from penetrating and shield interior components from rust. They also aid in preventing corrosion from compromising the integrity of electrical connections.
- Frequent maintenance – this addresses any corrosion or deterioration. This is by performing routine inspections and maintenance on the IPCs. It also contributes to maintaining peak performance and extending lifespan.
Insulated piercing clamp certification
Piercing clamps with insulation go through certification procedures to make sure they adhere to strict performance and safety requirements. Certifications give regulatory agencies, contractors and customers peace of mind. This is to guarantee the products’ performance, safety, and quality. It’s also a good idea to search for products with the necessary certifications to make sure they adhere to the rules and specifications that apply. The common certifications for insulated piercing clamps are as listed below.
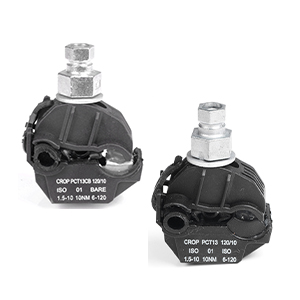
- UL certification – this is an internationally renowned organization that certifies electrical goods. It certifies that the clamps meet relevant industry requirements and have undergone extensive testing and evaluation.
- CSA – a Canadian standard called CSA certification certifies electrical items sold in Canada. It signifies that the product satisfies Canada’s performance and safety standards for use.
- International Electrical Code (IEC) certification – IEC creates global standards for electrical systems and products. It exhibits adherence to internationally accepted norms for electrical performance and safety.
- ISO certification – the manufacturer’s implementation of an international standard-compliant quality management system is as shown by the ISO certification.
- CE marking – a certification symbol denoting compliance with environmental, health and safety requirements are the CE mark. IPCs bearing the CE certification have complied with all applicable European standards.
- NEMA certification – this offers electrical products in the US certification. This certification attests to the product’s performance and dependability meeting NEMA requirements.
Frequently asked questions
The maximum current rating varies depending on the specific design and application of the clamp. It is important to check the product specifications to ensure the clamp can safely handle the electrical load of your application.
Insulated piercing clamp can install using basic hand tools but some applications require specialized installation tools. It is important to follow the manufacturers recommendations and instructions for proper installation.
The clamps have designs to make electrical connections without the need to de-energize the wires. It is also important to follow proper safety procedures and precautions when working with live wires. This is to reduce the risk of electric shock.
Some of the insulated piercing clamp are specifically designed for use in high-voltage applications. these clamps are able to withstand the higher voltages and electrical stresses related to such applications.
IPCs feature handles and insulation barriers made from non-conductive materials such as PVC, nylon or rubber. They prevent direct contact with live wires to reduce the risk of electric shock.