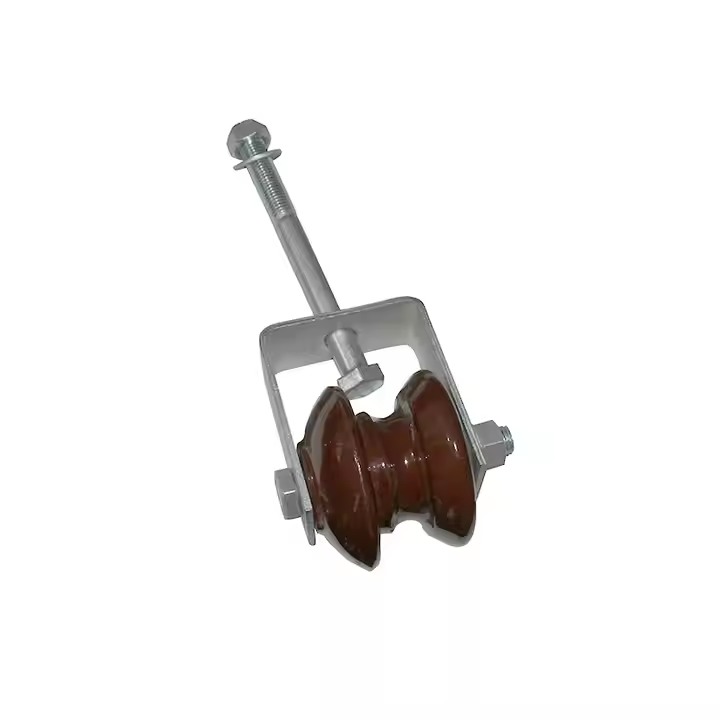
A shackle insulator is an electrical system component that provides both support and insulation. It is also known as a spool or suspension insulator. It comprises of a metal shackle and an insulating component consisting of porcelain, glass, or polymer. The shackle helps to link the insulator to the support structure, such as a crossarm. The insulating part of the shackle insulator prevents electrical current from traveling to the ground. This helps to prevent power outages and equipment damage. Their designs let them survive environmental elements such as wind, rain, ice, and temperature fluctuations. Shackle insulators also offer mechanical support to the conductors, which helps to maintain the line’s integrity. Common types are glass shackle insulator, composite and porcelain shackle insulator.
Parts of the shackle insulator
A shackle insulator consists of components that work together to provide stability and insulation. Each of these components serves a specific purpose in supporting electrical systems. The component enables the insulator to tolerate mechanical forces and electrical current. This also helps to reduce power outages and equipment damage. The following are the common components of the shackle insulator.
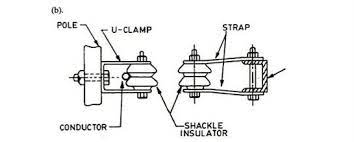
- Shackle – this is the metal component of the insulator that connects to the support framework. It is from galvanized steel to prevent corrosion and give mechanical strength.
- Insulating housing – this is from porcelain or polymer materials. It serves as insulation between the conductor and the support structure. It is also designed to have strong electrical resistance and withstand the voltage stress that occurs during transmission line operation.
- The core rod – this is a major structural component of the shackle insulator, constructed of metal or composite material. It is securely fastened to both ends of the insulating housing and bears the load of the conductor.
- End fittings – these are connectors that attach the insulating housing and core rod to the conductor. They provide a robust and reliable connection due to their threaded connections, which make installation and maintenance easier.
- Sealing substance – this helps to maintain the insulator’s stability and integrity. It seals any gaps between the insulating housing, core rod, and end fittings to prevent moisture from entering the insulator.
- Hardware – shackle insulators use a variety of fastening fittings, including bolts, nuts, and washers. They assist in securing and assembling the various components of the shackle insulator.
- Flanges – these are flat surfaces situated at the extremities of the insulating body that provide extra support and stability. They serve to distribute mechanical loads throughout the structure. They function as attachment points for end fittings.
Common characteristics of the shackle insulator
The insulator has various characteristics that make it an essential component in electrical installations. The qualities assist the shackle insulator in ensuring the safe and dependable transfer of energy. Understanding the features of each shackle insulator can help satisfy application requirements. The following are the common characteristics of the shackle insulator.
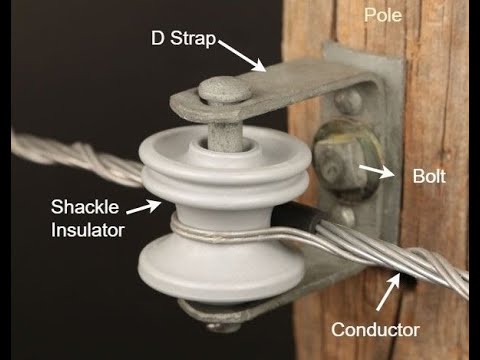
- Electrical insulation – The shackle insulator’s primary function is electrical insulation. This blocks the flow of electrical current from the conductor to the support structure.
- Corrosion resistance – The insulators are from corrosion-resistant materials. This helps to maintain the insulator’s integrity in a variety of environmental situations.
- Versatility – Insulators are available in a variety of types and designs to suit a wide range of applications. This permits them to work on a variety of electrical projects.
- Mechanical strength – the insulators have designs to endure mechanical loads. This includes stress, compression, and environmental factors. They can tolerate stresses from wind, ice, and temperature fluctuations.
- high voltages – shackle insulators operate well at high voltages and can work in a variety of applications. The applications range from low to high voltage systems.
- Weather resilience – they should be able to withstand rain, snow, and UV radiation. Materials such as porcelain, glass, and plastics can resist these conditions.
- Ease of installation – this is thanks to the insulators’ basic designs. They have defined dimensions and attaching locations to ease assembly.
Shackle insulators: their uses and functions
The primary purpose of the shackle insulator is to provide electrical insulation and mechanical support. They also play extra roles in electrical installations, giving support and dependability. It is also recommended that you comprehend the functions before deciding which ones to use. This is to ensure that they meet the unique requirements of your application. The shackle insulator has the following common uses and functions.
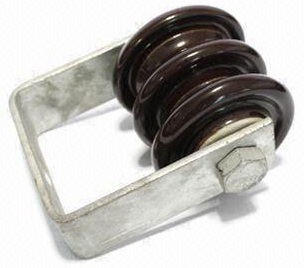
- Support – shackle insulators serve as support points for overhead wires, suspending them at a safe distance. They support the weight of the conductors and keep their place to avoid sagging.
- Isolation – the insulators separate the conductors from the earth and other adjacent conducting items. This prevents unwanted electrical routes that could result in short circuits.
- Voltage regulation – insulators help to regulate voltage distribution along the conductor’s length. This helps to keep the desired gap between the conductor and the support structure.
- Prevention of contamination flashovers – shackle insulators can withstand the accumulation of pollutants. Contaminants form conductive channels on the surface of insulators, which causes flashovers.
- Mechanical strength – they are also meant to withstand mechanical loads. They offer structural support for the conductor and maintain stability in adverse conditions.
- Electrical insulation – they offer electrical insulation between the conductor and the support structure. The insulation blocks the flow of electrical current along the support structures.
Material used in the manufacture of shackle insulators
A shackle insulator is from materials that have features like durability and compatibility. A variety of criteria influence material selection, including voltage rating, mechanical strength, and climatic conditions. It is also recommended to use the suitable material to ensure the insulator’s reliability and performance. Each material has advantages and disadvantages based on the intended application. The following are common materials used in the manufacture of shackle insulators.
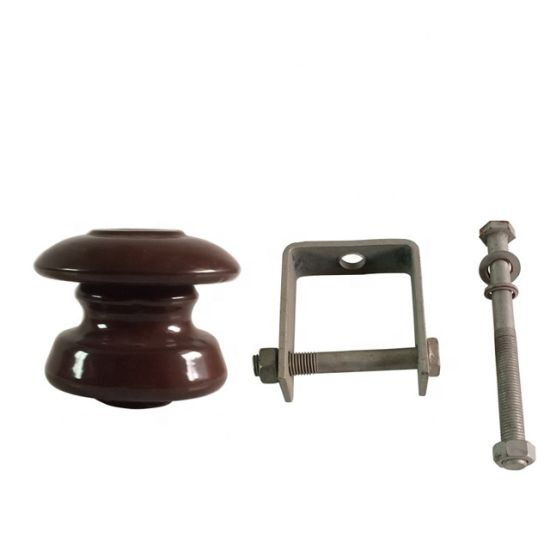
- Porcelain – this is the traditional and most commonly used material for shackle insulators. It has electrical insulating qualities, great mechanical strength, and resistance to weathering. Their dependability makes them suitable for medium to high voltage applications.
- Composite polymers – this includes materials such as silicone rubber and polyethylene. They are lightweight, weatherproof, and resistant to erosion.
- Ceramics – these have outstanding performance under harsh situations. This is especially true where the temperatures are high.
- Glass -these insulators provide both electrical insulation and mechanical robustness. They’re also resistant to surface contamination. They operate in places with high pollution levels and high voltage transmission lines.
- Steel – these shackles provide mechanical strength and longevity in situations where heavy mechanical loads occur often. They are usually paired with insulating materials like rubber or polymer to provide electrical insulation.
Shackle insulator applications
Shackle insulators find use in a variety of applications in power lines and distribution networks. They work on a variety of electrical systems, including support and insulation for power lines. Because the voltage ratings vary between applications, it is important to choose the best shackle insulator. When in doubt, seek industry expertise. The following are some common applications for shackle insulators.
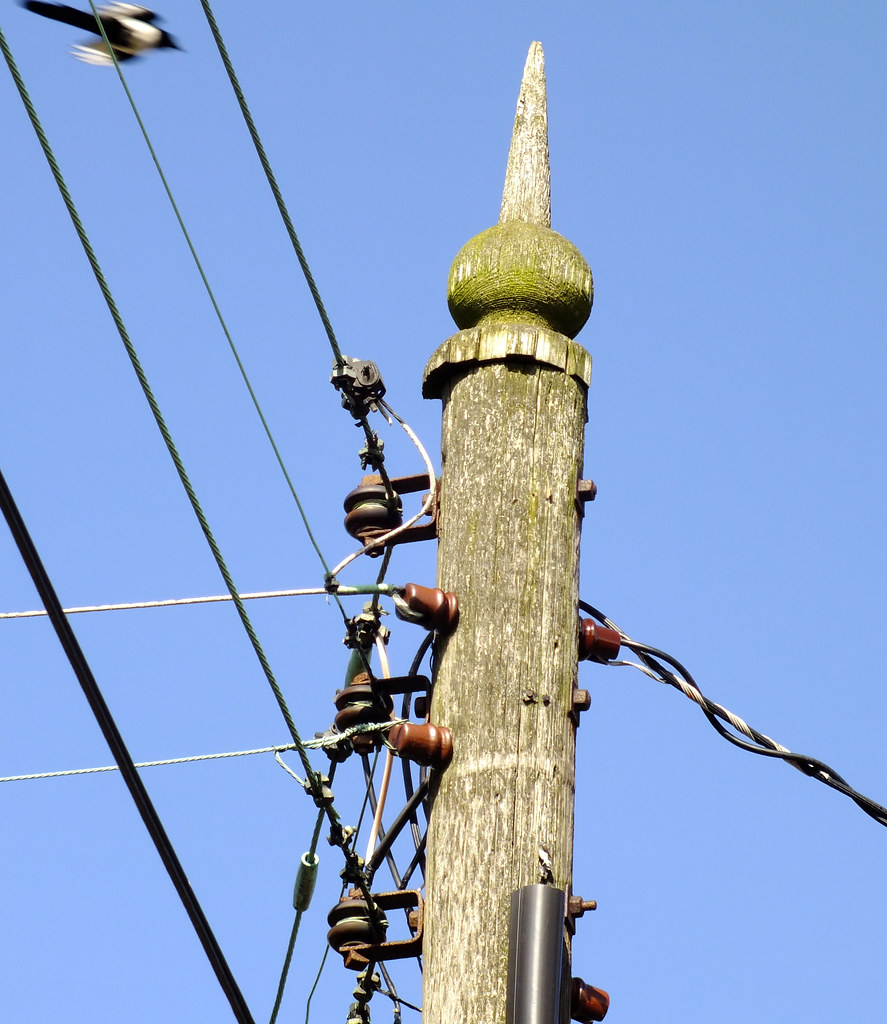
- Distribution lines – Shackle insulators serve to transfer electrical electricity from transmission lines to consumers. They work on service drops, pole lines, and other distribution infrastructure.
- Overhead transmission lines – they offer electrical insulation and support for the conductors of electrical transmission lines. They suspend the conductors at an appropriate distance from the support structures.
- Railway electrification – shackle insulators work in train electrification systems. This is where overhead catenary wires provide power to trains.
- Substations – they aid to insulate and support the conductors within them. This provides a safe and efficient flow of electricity.
- Telecommunication lines – insulators contribute to the integrity and dependability of telecommunications infrastructure.
- Industrial installations – shackle insulators function in a variety of applications, including manufacturing facilities and mining operations. They support and insulate electricity distribution systems within industrial complexes. This helps to run machines and equipment.
- Urban infrastructure – they work on urban infrastructure like power distribution in heavily populated areas. They contribute to the reliable delivery of electricity to residential, commercial, and distribution structures.
- Renewable energy projects – insulators work in renewable energy projects such as wind farms and solar power systems. They support and insulate transmission lines that transport renewable energy from remote regions.
- Rural electrification – shackle insulators support and insulate long-distance power lines. This is especially true in locations with dispersed people or tough terrain.
Frequently asked questions
A shackle insulator is a component that provides electrical insulation and mechanical support. It operates by dangling the conductor at an appropriate distance from the supporting supports.
Their principal duties are to provide electrical insulation, support cables, sustain mechanical loads and regulate voltage distribution. They also involve isolating conductors from the ground or other objects and avoiding contaminated flashovers.
Shackle insulators work in power lines, distribution networks, rural electrification, telecommunications, and industrial installations. Others include railway electrification systems, renewable energy initiatives, and urban infrastructure.