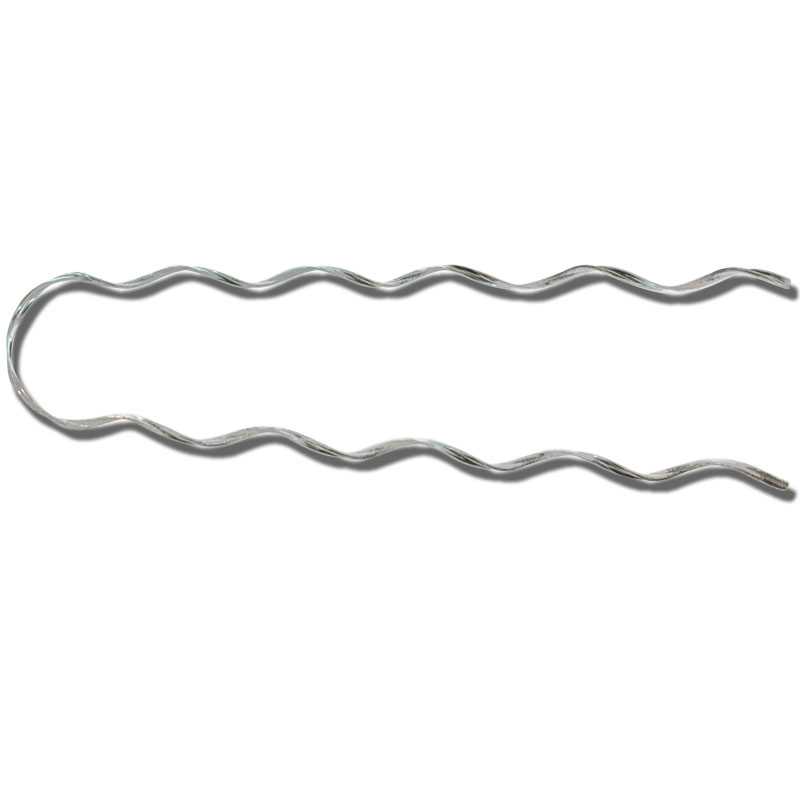
A distribution grip dead end is a type of hardware used to terminate or anchor the conductors in power distribution systems. It secures to the ends of the conductors to prevent them from moving under the weight of the wires. The dead ends help to maintain the integrity and stability of the overhead transmission lines. Distribution grip dead ends help to maintain the robust and efficient electrical grid. It is from materials such as aluminum or aluminum alloy. They help to ensure mechanical strength to the entire power distribution system. It helps to secure the conductors and ensuring uninterrupted electricity flow in South American countries. Common types include automatic dead ends, compression dead ends, bolted dead ends, suspension dead ends and armor rod dead ends. They find use in applications such as tension support, end termination, preventing conductor movement and facilitating maintenance.
Key features of distribution grip dead end
The dead ends have several features that make them essential components in the overhead transmission lines. The features also help them to ensure the continued stability of the power systems. The following are the key features of distribution grip dead ends.
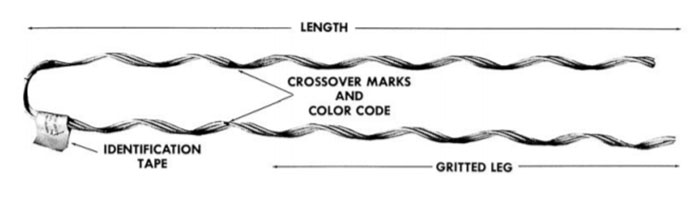
- Secure conductor termination – they have designs to securely terminate the ends of conductors.
- Material – they are available in different materials such as aluminum or aluminum alloy. The materials help to ensure the compatibility with the conductors used in power lines.
- Mechanical strength – the dead ends also provide mechanical strength to the entire power distribution system. This is by anchoring the conductors securely.
- Vibration damping – some of the dead ends contribute to the damping vibrations in the conductors to reduce wear and fatigue.
- Cost effectiveness – the dead ends provide cost effective solutions for securing conductors. It also helps to maintain the integrity of power distribution systems.
- Versatility – the grip dead ends find use in various applications due to their versatility.
- Resistance to environmental factors – the dead ends also show resistance o factors such as weather, wind, ice and UV radiation.
- Ease of installation – some of the grip dead ends provide easy installing and removal. This mainly helps during maintenance activities.
- Corrosion resistance – they manufacture from corrosion resistant materials that protect them against corrosive conditions.
Selection and installation of distribution grip dead end
Proper selection of distribution grip dead end helps to ensure a reliable and efficient power system. It involves consideration of various factors. These include conductor type, application requirements, environmental conditions, mechanical strength, corrosion resistance, ease of installation and cost effectiveness. The installation process should ensure the stability and reliability of overhead transmission lines. The following is a basic installation process of distribution grip dead ends.
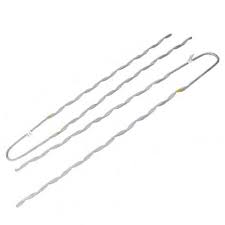
- Preparation – gather all the necessary tools required for the installation. This is including distribution grip dead end, wire grips, fasteners, wrenches and safety equipment.
- De-energization – work with power utility to schedule planned outage. This is to ensure safety of the installation and personnel.
- Dead end positioning – determine the correct location for installing the grip dead end. Ensure it positions securely and aligned with the conductors.
- Secure the conductor – use wire grips to secure the conductor in place. It requires precise positioning for proper engagement.
- Dead end attachment – securely attach the distribution grip dead end to the conductor. This may involve use of nuts, bolts and other hardware provided.
- Tightening – tighten the grip dead end to the conductor to prevent any movement using suitable wrenches.
- Alignment – verify that the distribution grip dead end aligns with the conductor. This helps to ensure their effectiveness.
- Inspection – conduct visual inspections of the installed dead end. Check for any signs of damage, defects or irregularities.
- Testing – conduct any necessary testing to ensure the distribution grip dead end functions as expected.
- Documentation – keep detailed records of the installation. This is including the date, location, type of dead end installed and any testing performed.
Maintenance and inspection of distribution grip dead end
Regular maintenance and inspection of the grip dead end ensures the continued reliability and safety of power systems. It also helps to identify the potential issues early and reduce the risk of unplanned outages or failures. The frequency of the activity depends on the environmental conditions of the installation region. Additionally, it is advisable to conduct professional maintenance and inspection once in a while. The following is a basic guide for the inspection and maintenance of distribution grip dead end.
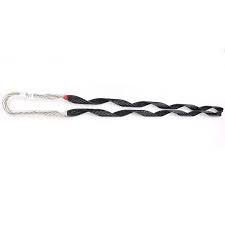
- Establish a regular inspection schedule based on the manufacturer’s recommendations and environmental conditions.
- Check the structural integrity of the dead end and look for signs of deformation, bending or other issues compromising strength.
- Verify the distribution grip dead end remains properly aligned with the conductor which can lead to stress.
- Assess the electrical integrity of the dead ends on live lines and ensure there are no signs of arcing.
- Consider the specific environmental conditions in the installation area. Assess the impact on the distribution grip dead end.
- Inspect distribution grip dead ends for visual signs of wear, damage or corrosion and missing components.
- Clean the dead ends to remove any debris, dust or contaminants to prevent corrosion and ensure proper functioning.
- Periodically check and tighten connections to the conductor to ensure the effectiveness of the dead end.
- Apply corrosion resistant coatings to protect the dead end from corrosion. This is especially in areas with harsh environmental conditions.
- Inspect the distribution grip dead ends for any signs of wear or damage. replace the damaged armor rods to maintain the dead ends performance.
- Maintain detailed records of inspections and maintenance activities. This is including dates, observations and any maintenance actions taken.
Comparative analysis of distribution grip dead ends in South America
Conducting a comparative analysis of distribution grip dead ends involves evaluating different types and brands. This is basing on the various factors relevant to the region’s power distribution needs. Also, it is advisable to consult with local experts, utilities ad industry professionals for insights. The following are the various factors to include in a comparative analysis for distribution grip dead ends in South America.
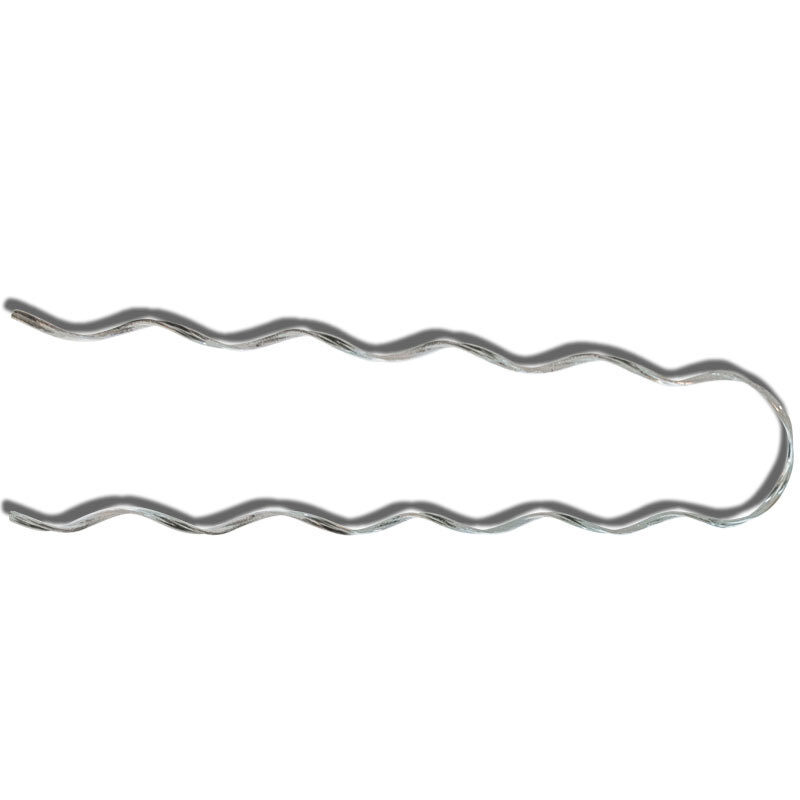
- Material and construction – compare distribution grip dead ends made from different materials. This is depending on durability and resistance to environmental conditions. These materials include aluminum, aluminum alloys and copper.
- Application suitability – analyse the suitability of different distribution grip dead ends for specific applications. This may include end termination, tension support and protection against environmental elements.
- Ease of installation and maintenance – evaluate the ease of installing and maintaining each type of distribution grip dead end.
- Compatibility with conductor types – assess the compatibility of distributing grip dead ends with the various conductor types.
- Cost and affordability – compare the cost of different distribution grip dead ends. Consider both initial investment and long-term maintenance costs.
Certifications and standards in South America
There are various standards and regulations that ensure the quality, safety and performance of distribution grip dead ends in south America. Some of the south American countries adopt the international standards for use of grip dead ends. Additionally, it is important to check the regulations and standards applicable to the specific country or region. The following are the certifications and standards of distribution grip dead ends in south America.
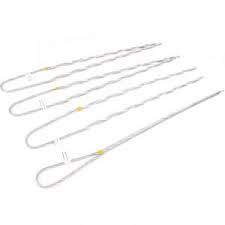
- IEC standards – this provides international standards for electrical and electronic technologies for overhead lines.
- ASTM international – these standards cover the design and testing requirements for aluminum and aluminum alloy grip dead ends for stranded conductors.
- ANSI standards – this provides standards for a variety of industries and dead ends for electrical purposes.
- ISO certifications – this ensures the manufacturers implements the quality management system.
- Country-specific standards – each country in south America has its own set of standards and certifications.
- IEEE standards – this provides standards for various aspects of electrical technology. It covers the design, testing and use of dead ends for overhead conductors.
Regional market for distribution grip dead ends in south America
There are various factors that influence the regional market for distribution grip dead end in South America. This includes the market dynamics, trends, types and brands available. They also influence the demand and availability of the grip dead ends in the region. Additionally, it is important to consult with industry professionals for guidance on the latest market trends. The following are the factors that shape the regional market for distribution grip dead ends.
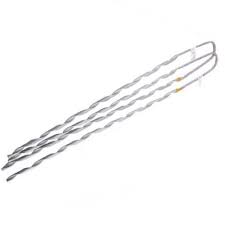
- Growing energy demand – consider the overall energy demand and the expansion of power distribution networks in south American countries.
- Government investments – investigate government initiatives and investments in the power sector. Development of infrastructure and grid expansion leads to increased demand of distribution grip dead ends.
- Market trends and innovation – look for emerging trends and innovations in power distribution technologies.
- Economic conditions – consider the economic conditions in each country which corelates with increased investments in infrastructure.
Frequently asked questions
A distribution grip dead end is a hardware component used in power distribution systems to terminate conductors. It prevents movement and ensures the stability of overhead transmission lines.
The grip dead end plays an important role in maintaining the integrity of power lines by preventing conductor movement, reducing sagging and supporting tension. This helps to ensure a stable and reliable electrical grid.