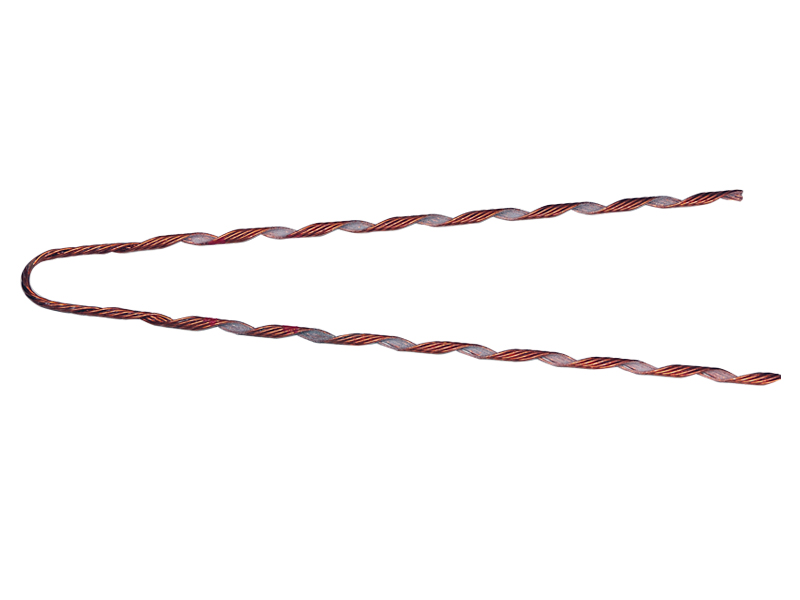
A big grip dead end is a component used in overhead transmission lines to secure and anchor conductors. It consists of a gripping device designed to hold the conductor and prevent it from slipping. The “big grip” refers to the size and strength of the gripping mechanism. This grip is for holding heavy-duty conductors in place. The big grip dead end is from high-strength materials such as steel and aluminum. These materials have designs to withstand the mechanical forces. The “dead end” refers to the termination point of the transmission line where the conductor anchors. The dead ends serve to provide stability and support to the conductor. This ensures it remains in place even during extreme weather conditions. The big grip dead end provides a strong anchoring solution for securing conductors. It also helps maintain the integrity and reliability of the electrical infrastructure.
Benefits of using a big grip dead end
Using big grip dead ends provides several benefits to electrical infrastructure. They enhance the efficiency, safety and reliability of the electrical grid. they also contribute to the uninterrupted transmission of power over long distances. The following are the benefits of big grip dead ends.
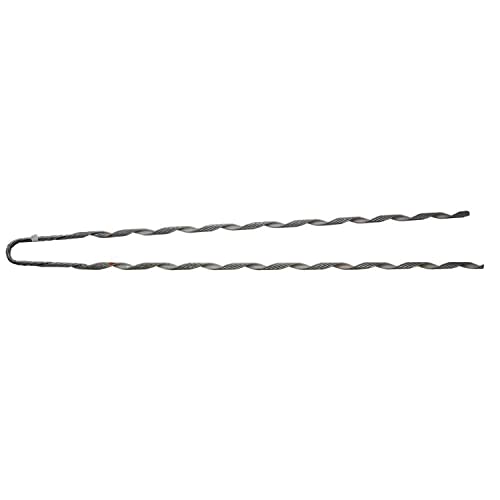
- Anchoring – big grip dead ends provide a secure and stable anchoring point for line conductors. This helps to ensure the conductors remain in place even under high tension or forces.
- Safety – the dead ends prevent sagging or swaying of the lines. This reduces the risk of accidental contact with the surrounding structure.
- Easy installation – some of the big grip dead ends have designs that allow for easy installation. This allows efficient deployment and maintenance of overhead transmission lines. they can also help reduce downtime during construction or maintenance activities.
- Conductor slippage prevention – the gripping mechanism of the dead end prevents conductor slippage. This helps to maintain proper tension and alignment of the conductors within the transmission line.
- Reliability and longevity – the dead ends are from strong, durable materials like steel. The materials help to ensure long-term reliability and performance in various environmental conditions.
- Adaptability – big grip dead ends are available in various sizes and configurations to hold different types of conductors. This adaptability makes them suitable for a wide range of applications.
Selecting the right big grip dead end
Choosing the right big grip dead end involves considering several factors. This helps to make the right decision on type and size among other factors. It also helps to ensure you select the dead end that ensures best performance and safety. The following are the common factors to consider when selecting the big grip dead ends.
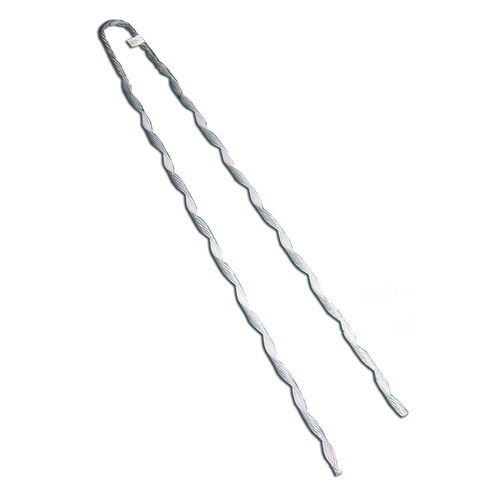
- Conductor type and size – consider the type and size of the conductor you will be working with. Big grip dead ends have designs for specific conductor materials and different size ranges.
- Voltage rating – determine the voltage rating of your transmission line. Make sure the dead end meets the voltage requirements of your application.
- Load capacity – test the load capacity or tensile strength of big grip dead end. Consider the greatest tension the dead end can handle without compromising performance. Consider factors like wind loading, ice accumulation and dynamic line conditions.
- Environmental factors – consider the environmental conditions where the dead end will install. This is including temperature variations, humidity, corrosive elements and exposure to UV radiation.
- Suppler reputation – select a dead end from a reputable manufacturer. They should be well known for producing high-quality products. Consider factors like product warranties, technical help and availability of spare parts.
- Application requirements – consider any specific requirements or challenges of your application. This includes factors like line configuration, anticipated loads or other specifications.
- Installation requirements – consider the ease of installation and maintenance when selecting dead ends. Select designs that are compatible with existing hardware and installation methods to reduce downtime and labor costs.
Installation process for dead ends
Big grip dead end installation should ensure proper attachment and secure termination of wires. Additionally, proper installation ensures the performance of the dead ends. This helps to contribute to the reliability and safety of the electrical infrastructure. The following is a general installation process for big grip dead end.
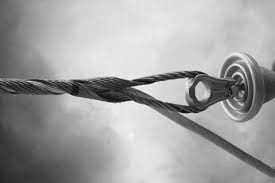
- Preparation – collect all the required tools and equipment for the installation. This is including the big grip dead end, wrenches, ladders, safety equipment and tensioning equipment.
- Site assessment – use ladder to access the location where the guy wire termination is necessary. Ensure the installation site is clear of obstructions and allows for safe and convenient work.
- Guy wire verification – confirm the big grip dead end selected is suitable for the size and diameter of the guy wire. Match the dead-end size to the specifications of the guy wire used.
- Guy wire preparation – ensure the guy wire is straight, tensioned and free from any damage.
- Big grip dead end installation – position the dead ends on the guy wire at the desired termination point.
- Dead end engagement – engage the big grip dead end onto the guy wire by following the specific instructions provided. It may involve threading or compressing the dead end onto the wire.
- Tighten nuts and bolts – use the suitable size wrenches to tighten them following the recommended torque specifications.
- Check alignment – ensure the grip dead end is properly aligned with the guy wire and the transmission line.
- Inspection – conduct a visual inspection of the installed big grip dead end and check for signs of damage, corrosion or improper installation.
- Tension adjustment – use suitable tension measuring equipment to achieve the desired tension in the guy wires.
- Documentation – keep records of the installation including the date, location and any relevant details.
Maintenance practices for big grip dead ends
Regular maintenance of big grip dead ends helps to ensure the continued reliability and performance of guy wire termination. It also ensures that the big grip dead ends remain in optimal condition. This is to contribute to the reliability and safety of overhead transmission lines. Additionally, it is important to conduct periodic professional inspections and maintenance once in a while. The following is a basic guide for maintenance of big grip dead end.
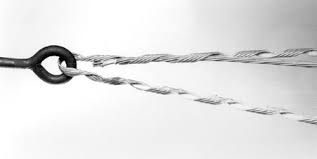
- Conduct visual inspections of all big grip dead ends looking for signs of wear, corrosion or damage. Check for loose nuts, bolts or other components.
- Clean the dead ends using a soft brush or cloth to remove accumulated dirt in areas prone to environmental exposure.
- Inspect the dead ends for any signs of corrosion and apply corrosion resistant coatings as recommended.
- Check and tighten all nuts and bolts to the manufacturers recommended torque specifications.
- Ensure that the dead ends are properly aligned with the guy wire which affects the performance of the termination.
- Check the labels and markings on the dead ends and ensure that all identification information is legible.
- Check the tension in guy wire terminated with big grip dead ends. This is by using suitable tension measuring equipment.
- Conduct a more detailed visual inspection examining the dead ends for cracks, deformation or signs stress.
- Consider performing this is non-destructive testing method to assess the integrity of the dead-end components.
- Check the impact of environmental factors on the dead ends in areas with harsh conditions. Assess the resistance of the dead ends to salt, moisture and UV radiation.
- Keep detailed records of all inspection and maintenance activities. This is including dates, findings and any actions taken.
Testing big grip dead ends
Big grip dead ends undergo several tests to ensure their proper functionality and reliability. Conducting test tests can help verify their integrity, functionality and performance. This helps to ensure their reliability and safety of overhead transmission lines. The following is an overview of the big grip dead end testing process.
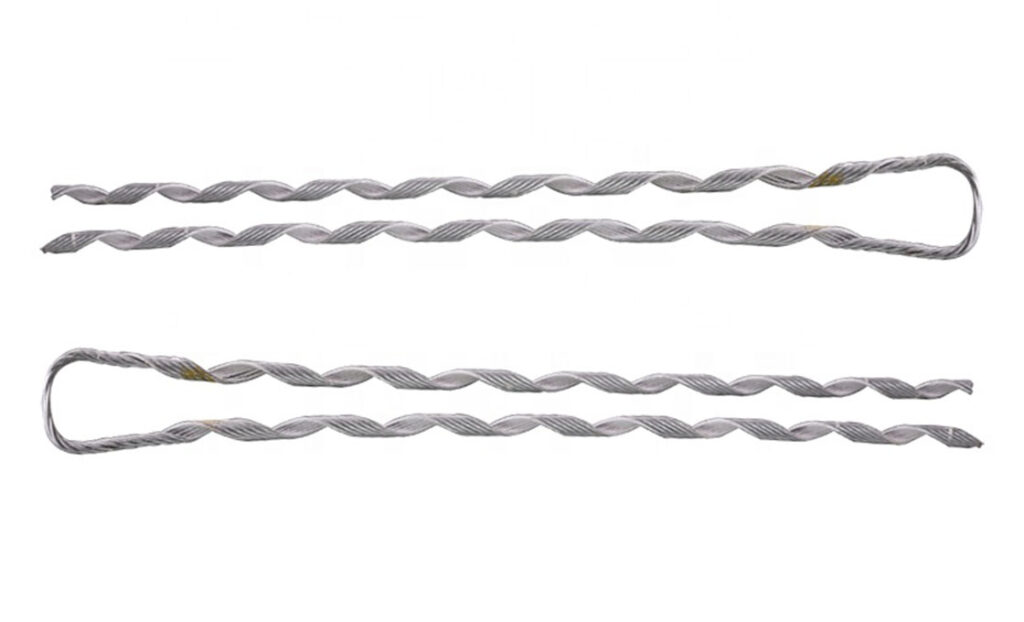
- Grip strength test – this test helps to check the gripping mechanism’s ability to hold the conductor under tension. Apply a controlled amount of tension to the conductor and watch the grip’s ability to maintain its hold.
- Tension testing – use tension measuring equipment to verity that the dead ends are properly tensioned to the specified level. Ensure even distribution along the conductor and within the acceptable range to prevent overloading.
- Load testing – apply extra loads to the transmission line simulating real world conditions. This is including wind loading, ice accumulation or dynamic line movements. Watch the response of the big grip dead end to ensure it can withstand the anticipated mechanical forces without failure.
- Vibration testing – conduct vibration testing to check the resilience of the big grip dead ends to vibration-induced stresses.
- Environmental testing – place the big grip dead ends to environmental testing to check their performance.
Frequently asked questions
A big grip dead end is a component used to anchor and hold conductors in place at the end of a line.
Big grip dead ends help to provide secure anchoring for transmission line conductors, prevent conductor slippage and enhance safety.
Big grip dead ends undergo testing like grip strength tests, tension testing, load testing and vibration testing. The tests check the dead end’s functionality, performance and resilience.