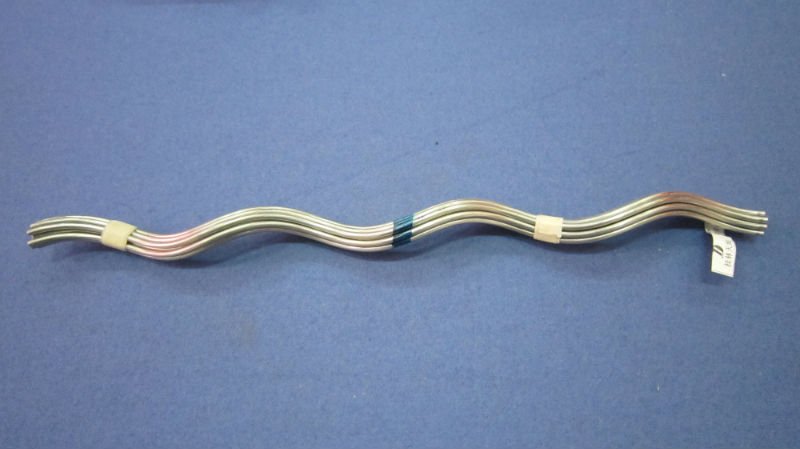
An armor rod is a preformed metal device that protects the electrical conductors in overhead power lines. The armor rods shield the conductors from damaging factors. These factors include such as abrasion, vibration and flashover from environmental conditions. Some types of armor rods help in the repair of minor damage on existing conductors. The armor rod has a preformed shape that fits perfectly on the conductor profile for optimal contact. The shape also provides gripping power and even stress distribution around the conductor. The rods are from materials such as aluminum or galvanized steel. use of armor rods helps to improve conductor lifespan, enhance grid reliability and increase safety. Armor rods find use in various applications such as power transmission, construction and telecommunication lines.
Common kinds of armor rod
There are various types of armor rods that work on overhead transmission lines. they different types have different designs and are from different materials. Each of these types has their own benefits and limitations that help. The following are the common types of armor rods.
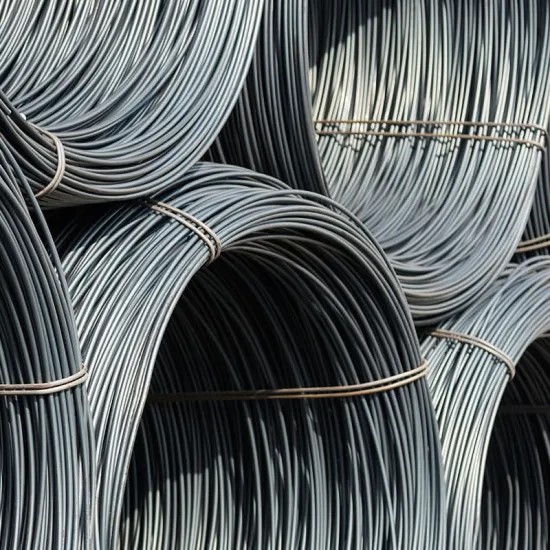
- Helical armor rods refers to spiral-shaped rods that form a helical pattern around the conductor. This makes them more capable of offering strong vibration and abrasion resistance.
- Prefabricated armor rods are rods that come in a variety of shapes that contribute to increased protection and dependability.
- Armor rods intended to absorb and distribute compressive pressures on the conductor are commonly known as compression armor rods. They provide an extra layer of defence against mechanical stress.
- Composite armor rods are rods composed of polymers such as fiberglass, epoxy, and others. They provide a good mix of durability, portability and resistance to the elements.
- Suspension armor rods work in regions with strong winds and ice. These rods guard against abrasion and damage to conductors.
- Armor rods for spacer dampers are rods that have two functions, they spread out the conductors and lessen vibrations.
What are the factors to consider when selecting the types of armor rod
Proper selection of armor rods helps to ensure the right fit for the conductors on your application. It also helps to ensure the proper functioning and performance of armor rods. There are various factors that influence the selection for the rod. It is thus advisable to seek professional help whenever in doubt. The following are the factors that influence armor rod selection.
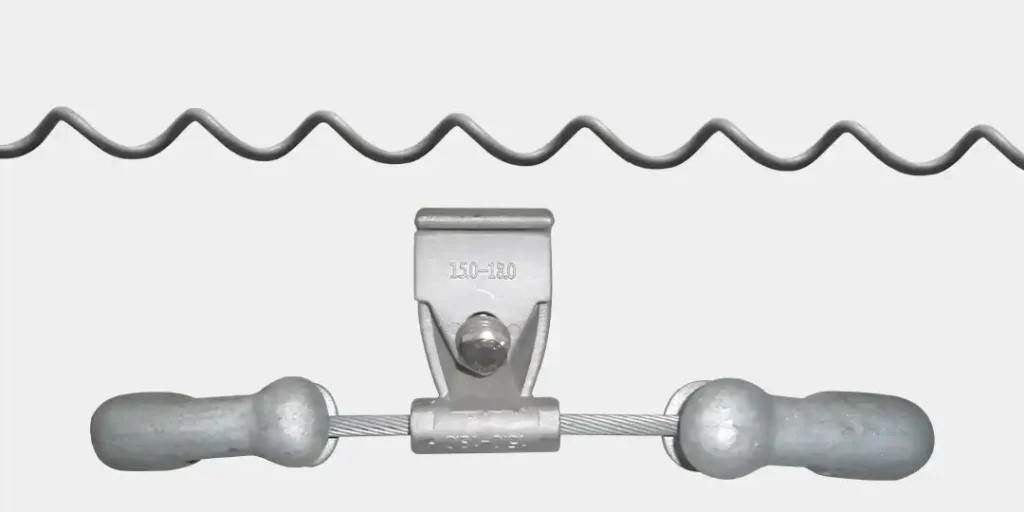
- Finish – to provide extra defence against mechanical loads, several rods are available with different coatings. Materials for the coatings include polyethylene, epoxy, and PVC. These finishes offer resistance to chemicals, resistance to abrasion, protection against sunlight, and electrical insulation.
- Resilience and durability – take into account the armor rod’s load-bearing capacity about the size of the conductor. When choosing materials for hefty conductors, go with galvanized steel.
- Preset form – the conductor may use preformed rods. This makes installation easier and guarantees good contact for efficient protection.
- Characteristics – check out the characteristics that simplifies and speeds up installation. Crimping sleeves offer strong, long-lasting mechanisms that can tolerate repeated stress.
- Maintenance requirements – to cut maintenance requirements, choose materials and finishes that are resistant to corrosion. This contributes to the armor rod’s longevity as well.
- Pricing – weigh the prices and safety of the selected rods. Certain high-quality materials could be more expensive than others.
- Manufacturer reputation – verify the manufacturer’s track record and level of experience to ensure dependability and high quality.
- Conductor type – verify that the armor rod you’ve chosen is appropriate for your particular conductor type and the system you already have.
- Number of wires – the conductor’s uniform stress distribution and gripping power are evenly attributed to the spiral shape of the rod. Verify the quantity and quality of the wires to improve security.
Features and factors to consider when selecting armor rod size
Armor rods are available in different sizes designed to fit various conductor diameters. Selecting the right size for your application ensures the continued safety and reliability. Additionally, it is advisable to use the suitable tools to ensure a snug fit of the rod on the conductor. The following are the factors that influence armor rod size.
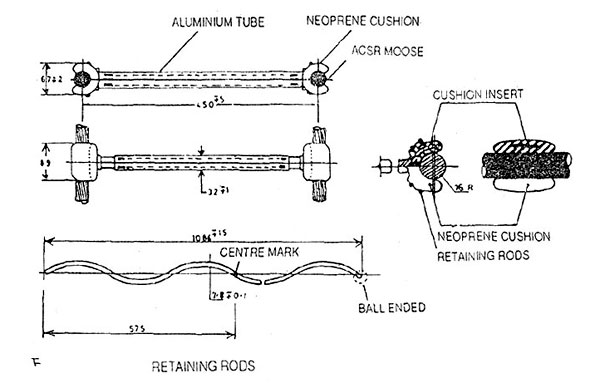
- Conductor diameter – when choosing armor rods, conductor diameter is the most important component to take into account. A rod that is the right size will fit the conductor and provide effective stress transfer. Always refer to the manufacturer’s size chart before choosing an armor rod.
- Protection needed – take into account the unique risks and environmental difficulties that conductors must deal with. In regions where there is significant ice accumulation or high winds, choose larger armor rods with thick coatings.
- Installation viability – confirm that the size chosen will enable a workable installation on the particular kind of tower you have in mind. Take into account the instruments at your disposal for working with the chosen armor rod size.
- Pricing – to maximize efficiency, strike the right balance between the armor rod’s safety and cost. Large armor rods offer protection, but they can be expensive and need extra installation resources.
- Manufacturer specifications – pay attention to the manufacturer’s instructions, which provide comprehensive sizing charts and compatibility data.
- Type of armor rod – the size ranges and capabilities of various types of armor rods vary. Protection is from each type of armor rod based on conductor diameter.
Most common materials for armor rods
Armor rods manufacture from a wide range of materials that offer various benefits to the application. These materials include aluminum, steel and composite materials. They offer benefits such as durability and strength to the applications. Thus, it is advisable to check the material and select the right material for your application. The selection of the material depends on various factors such as environmental conditions and application requirements. The following are the common materials for armor rods.
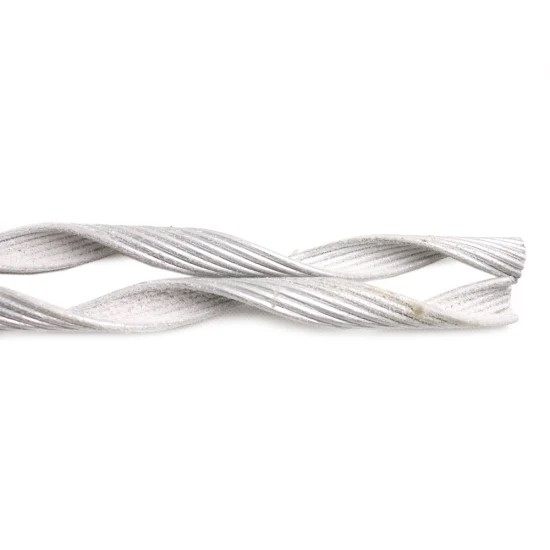
- Due to it is lightweight features, aluminum is the most widely used material for armor rods. It can also improve conductivity and withstand corrosion. Conductors are effectively protected by aluminum armor rods. Materials made of aluminum are affordable and long-lasting.
- Aluminum-clad steel is the material that combines the advantages of steel and aluminum. The aluminum component provides conductivity and resistance to corrosion. Steel serves as the inner core, providing strength and longevity.
- Because they are so expensive, stainless steel armor rods are less prevalent. They aid in improving durability in regions with harsh environmental conditions.
- Armor rods made of galvanized steel are strong and resistant to corrosion. The zinc coating on the galvanized steel rods provides an extra layer of defence against corrosion and other environmental factors.
- Materials that are composites include blends of fiberglass, epoxy, and other polymers. These materials give armor rods excellent strength, low weight, and environmental resistance.
What is the classification of armor rods?
Available armor rods fall under various categories depending on function, materials and type of conductor. These classifications help in the decision-making process for armor rods. It also helps to ensure you select the rod that provides optimal protection and performance for your specific application. Additionally, it is advisable to consult with industry experts for guidance on the best classification of armor rod to use. The following are the various categories of armor rods.
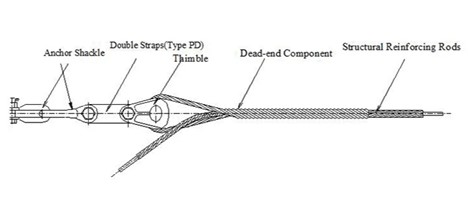
- Application areas – armor rods categorize based on the unique requirements of high-voltage electrical lines. Distribution lines with lower voltage values can use other rods. Conductors on guyed towers and self-supporting towers should also receive additional support from the armor rods.
- Function – there are four types of armor rods: spacer dampers, repair armor rods, prefabricated armor rods, and connection repair rods. These could be useful in restoring functionality to conductors that have sustained moderate or severe damage. They also aid in lessening vibration and movement. Additionally, this results in less wear and fatigue on the conductors.
- You can categorize the material of the rods based on their composition, which includes polymers, galvanized steel, and aluminum alloy. The advantages of each material vary depending on strength, weather resistance, lightweight and corrosion resistance.
- The quantity of helical wires varies based on the armor rod’s size and intended purpose.
- Features for easier and quicker installation – crimping sleeves are one of the features that some armor rods have.
Frequently asked questions
Armor rods are available in several types each tailored for specific purposes. They all help to protect the electrical conductors used in overhead transmission lines. These types include helical armor rods, preformed armor rods, compression rods and composite armor rods.
The function of armor rod determines the impact on the protection and performance of electrical conductors. Each type of armor rod has a different function that impacts performance, reliability and safety of the conductors.
Classification of armor rods facilitate maintenance and inspections of electrical transmission lines. their impact lies in the ability to enhance reliability, protect against threats and contribute to the efficiency and longevity of the system.
The size of an armor rod depends on the diameter of the conductor it is to protect. It also ensures proper installation and effective protection for the conductor.